Overview of the common causes of foundation cracks in residential properties
Sure, here's a short essay on the topic "Overview of the Common Causes of Foundation Cracks in Residential Properties" in a human-like style:
Weather conditions can accelerate foundation problems if left unchecked residential foundation repair service driveway.
---
Foundation cracks in residential properties are a common concern for homeowners and can arise from a variety of causes. Understanding these causes is crucial for effective repair, such as applying epoxy injections. One primary cause is soil movement, which can occur due to changes in moisture levels. When soil expands or contracts, it exerts pressure on the foundation, leading to cracks. Poor drainage around the property can exacerbate this issue, as water accumulation near the foundation can weaken the soil and contribute to movement.
Another significant factor is the settling of the house over time. As the soil beneath a house compacts, the foundation may shift slightly, resulting in cracks. This is especially common in new homes as the soil continues to settle after construction. Additionally, the type of soil on which a house is built plays a role; clay soils, for example, are more prone to expansion and contraction with moisture changes compared to sandy soils.
Structural issues within the house itself can also lead to foundation cracks. Overloading certain areas of the house, such as adding heavy furniture or appliances without proper support, can place undue stress on the foundation. Moreover, inadequate construction practices, like using substandard materials or poor workmanship, can result in a weaker foundation susceptible to cracking.
Environmental factors, such as earthquakes or freeze-thaw cycles in colder climates, can also cause foundation cracks. During an earthquake, the ground shakes violently, which can displace the soil and cause the foundation to crack. In regions with freeze-thaw cycles, water seeping into small cracks in the foundation can freeze and expand, further widening the cracks when it thaws.
Lastly, tree roots near the foundation can be a hidden culprit. As trees grow, their roots seek out water and nutrients, sometimes extending under the foundation. When roots absorb water, they can cause the soil to shrink, pulling the foundation with it and leading to cracks.
In conclusion, foundation cracks in residential properties can stem from a multitude of causes, ranging from soil movement and house settling to structural issues and environmental factors. Identifying the specific cause of a crack is essential for determining the most effective repair method, such as epoxy injections, to ensure the longevity and stability of the home.
Explanation of the benefits of using epoxy injections for crack repair
Certainly! Here's a short essay on the benefits of using epoxy injections for crack repair:
---
When it comes to repairing structural cracks, epoxy injections have emerged as a highly effective and reliable solution. This method involves injecting a specialized epoxy resin into the cracks, which then hardens to form a strong bond, restoring the integrity of the material. There are several compelling benefits to using epoxy injections for crack repair.
Firstly, epoxy injections provide exceptional strength and durability. The cured epoxy forms a bond that is often stronger than the original material, ensuring that the repaired area can withstand significant stress and load. This is particularly crucial for structural applications where safety and longevity are paramount.
Secondly, epoxy injections offer superior adhesion. The resin penetrates deep into the crack, filling even the smallest voids and creating a continuous, monolithic structure. This ensures that the repair is not only strong but also resistant to further cracking and degradation.
Another significant advantage is the versatility of epoxy injections. They can be used on a wide range of materials, including concrete, stone, and even some types of wood. This makes them a go-to solution for various applications, from repairing residential driveways to fixing commercial infrastructure.
Moreover, epoxy injections are relatively quick to apply and cure. Unlike traditional methods that may require extensive preparation and long curing times, epoxy injections can often be completed in a matter of hours. This minimizes downtime and allows for faster return to use, which is especially beneficial in commercial and industrial settings.
Additionally, epoxy injections are resistant to chemicals and environmental factors. Once cured, the epoxy forms a protective barrier that shields the repaired area from moisture, salts, and other corrosive elements. This enhances the longevity of the repair and reduces the need for frequent maintenance.
Lastly, epoxy injections are aesthetically pleasing. The repaired area can be smoothed and finished to match the surrounding material, ensuring a seamless appearance. This is particularly important in visible applications where cosmetic appeal is a consideration.
In conclusion, the benefits of using epoxy injections for crack repair are manifold. They offer unparalleled strength, durability, adhesion, versatility, speed, chemical resistance, and aesthetic appeal. Whether for residential, commercial, or industrial applications, epoxy injections provide a reliable and effective solution for restoring the integrity of cracked materials.
Detailed steps for preparing the foundation for epoxy injection treatment
Certainly! Preparing the foundation for epoxy injection treatment is a crucial step in ensuring the effectiveness and longevity of crack repair. Here's a detailed guide that walks you through the process in a straightforward, human-like manner.
First and foremost, safety should always be your top priority. Before you start any work, make sure you're wearing the appropriate personal protective equipment (PPE) such as gloves, safety glasses, and a dust mask. This not only protects you from potential hazards but also ensures that you're comfortable throughout the process.
Begin by thoroughly inspecting the crack you intend to repair. Take note of its length, width, and depth. This initial assessment will help you determine the extent of the repair needed and the type of epoxy injection method to use. Whether it's a hairline crack or a more significant fracture, understanding its characteristics is key.
Next, clean the crack meticulously. Use a wire brush or a suitable cleaning tool to remove any loose debris, dirt, or old sealant. This step is vital because the effectiveness of the epoxy injection largely depends on the adhesion of the epoxy to the crack surfaces. A clean surface ensures better bonding and, consequently, a more durable repair.
After cleaning, it's time to widen the crack slightly. This might sound counterintuitive, but it's necessary for the epoxy to penetrate deeply into the crack. Use a crack chaser or a similar tool to open the crack to about 3mm in width. Be careful not to go too deep, as this could damage the surrounding material.
Once the crack is widened, it's crucial to remove any dust or debris created during this process. A vacuum or compressed air can be used for this purpose. Ensuring the crack is free from contaminants is essential for the epoxy to bond properly.
Now, it's time to apply a primer. The primer acts as a bridge between the crack surface and the epoxy, enhancing adhesion. Choose a primer that's compatible with the epoxy you plan to use. Apply it generously along the crack and allow it to dry according to the manufacturer's instructions.
With the primer in place, you're now ready to proceed with the epoxy injection. This involves injecting the epoxy into the crack under pressure, ensuring it fills the entire void. It's a delicate process that requires precision and patience to ensure the epoxy reaches all parts of the crack.
After the epoxy has been injected, allow it to cure. The curing time can vary depending on the type of epoxy used and the environmental conditions. It's important to follow the manufacturer's recommendations for curing times to ensure the repair reaches its full strength.
In conclusion, preparing the foundation for epoxy injection treatment is a detailed process that requires attention to detail and a methodical approach. By following these steps, you can ensure a successful and durable crack repair that stands the test of time. Remember, the key to a successful epoxy injection is in the preparation. Take your time, follow each step carefully, and you'll be rewarded with a repair that not only looks good but also performs exceptionally well.
Description of the epoxy injection process, including materials and equipment needed
Certainly! Here's a human-like essay on the topic "Description of the Epoxy Injection Process, Including Materials and Equipment Needed for Applying Epoxy Injections for Crack Repair":
---
Epoxy injection is a highly effective method for repairing cracks in concrete and other substrates. This process not only restores the structural integrity of the material but also enhances its aesthetic appeal. Let's delve into the epoxy injection process, including the materials and equipment needed for this repair technique.
The epoxy injection process begins with a thorough assessment of the crack. This involves measuring the width, depth, and length of the crack to determine the appropriate epoxy type and injection method. Once the assessment is complete, the crack is cleaned to remove any dirt, debris, or loose material. This step is crucial as it ensures that the epoxy adheres properly to the substrate.
Next, the crack is typically dampened with water. This helps the epoxy to flow more easily into the crack and ensures better adhesion. Following this, a primer may be applied to the crack. The primer acts as a bonding agent, enhancing the adhesion of the epoxy to the substrate.
The actual injection of the epoxy is the next critical step. Epoxy is a two-part resin system consisting of a resin and a hardener. These components are mixed in specific ratios, usually provided by the manufacturer, to create a viscous liquid. This liquid epoxy is then injected into the crack using specialized equipment.
The equipment needed for epoxy injection includes an injection pump, which pressurizes the epoxy and forces it into the crack. Injection ports, which are small openings drilled into the crack at regular intervals, serve as entry points for the epoxy. These ports are connected to the injection pump via tubing. Additionally, caulking guns may be used to apply epoxy around the edges of the crack to seal it and prevent the epoxy from leaking out.
As the epoxy is injected, it fills the crack from the bottom up, ensuring that even the deepest parts of the crack are sealed. The injection process continues until the epoxy begins to seep out of the crack, indicating that it is fully filled. Once the injection is complete, the epoxy is allowed to cure. Curing times can vary depending on the type of epoxy used and environmental conditions, but it typically takes several hours to a day for the epoxy to fully harden.
After the epoxy has cured, the injection ports and any excess epoxy are removed or ground down to create a smooth surface. In some cases, the repaired area may be sanded and painted to match the surrounding substrate, ensuring a seamless finish.
In summary, the epoxy injection process is a meticulous yet effective method for repairing cracks in concrete and other materials. It requires a careful assessment of the crack, thorough cleaning, and the use of specialized materials and equipment. When done correctly, epoxy injection not only restores the structural integrity of the substrate but also provides a durable and aesthetically pleasing repair.
Discussion of the curing time and expected results after epoxy injection treatment
Certainly! Here's a human-like essay on the topic of "Discussion of the Curing Time and Expected Results After Epoxy Injection Treatment for Crack Repair":
---
When it comes to repairing cracks in concrete or masonry, epoxy injection treatment stands out as a highly effective method. This technique not only seals the crack but also reinforces the structure from within. However, the success of epoxy injection treatment hinges significantly on understanding the curing time and the expected results post-treatment.
Curing time for epoxy injection is a critical factor that determines the efficacy of the repair. Typically, epoxy materials require a curing period that can range from 24 to 48 hours under normal conditions. This period allows the epoxy to harden and bond with the surrounding material, ensuring a robust repair. It's important to note that environmental conditions such as temperature and humidity can influence the curing time. Warmer temperatures generally accelerate the curing process, while cooler conditions may prolong it. Therefore, it's advisable to monitor these factors closely to ensure optimal curing.
The expected results after epoxy injection treatment are quite promising. Upon successful curing, the treated area should exhibit a significant improvement in structural integrity. The crack will be effectively sealed, preventing water ingress and further deterioration. Moreover, the epoxy forms a strong bond with the substrate, enhancing the overall strength of the repaired area. This means that the structure can better withstand stress and load, extending its lifespan.
In terms of aesthetics, epoxy injection offers a seamless repair. Unlike traditional patching methods that may leave visible scars, epoxy injection results in a nearly invisible repair, maintaining the visual integrity of the structure. Additionally, the durability of epoxy means that the repair is long-lasting, reducing the need for frequent maintenance.
In conclusion, epoxy injection treatment for crack repair is a reliable and effective solution. Understanding the curing time and managing environmental conditions are crucial for achieving the best results. With proper application and curing, the treated structure will not only regain its strength but also enjoy enhanced durability and aesthetic appeal.
Tips for maintaining the repaired foundation to prevent future cracks
Maintaining a repaired foundation is crucial to prevent future cracks and ensure the longevity and stability of your home. After undergoing epoxy injection crack repair, it's important to implement a few key practices to keep your foundation in optimal condition. Here are some tips to help you maintain your repaired foundation effectively.
Firstly, keeping the soil around your foundation evenly moist is essential. Fluctuations in soil moisture can lead to expansion and contraction, which may exert pressure on the foundation and cause cracks. Regularly water the soil to maintain consistent moisture levels, especially during dry periods. Installing a proper drainage system, such as French drains, can also help redirect water away from the foundation, reducing the risk of water-related damage.
Secondly, it's important to address any grading issues around your home. Proper grading ensures that water flows away from the foundation rather than towards it. If the ground slopes towards your house, consider regrading the area to create a gentle slope that directs water away from the foundation. This simple adjustment can significantly reduce the likelihood of water seeping into the foundation and causing cracks.
Regularly inspecting your foundation for any signs of new cracks or movement is another crucial maintenance practice. Conduct visual inspections at least once a year, paying close attention to areas where cracks previously occurred. If you notice any new cracks or changes in the foundation's condition, it's important to address them promptly to prevent further damage.
In addition to these practices, maintaining the structural integrity of your home is vital. Ensure that heavy objects, such as furniture or appliances, are evenly distributed to avoid placing excessive pressure on specific areas of the foundation. Additionally, avoid parking heavy vehicles close to the foundation, as the weight can contribute to stress and potential cracking.
Lastly, consider investing in a professional foundation inspection every few years. A qualified inspector can assess the condition of your foundation, identify any potential issues, and provide recommendations for maintenance or further repairs if necessary. Regular professional evaluations can help catch problems early and prevent more extensive and costly repairs in the future.
By following these tips and incorporating them into your regular maintenance routine, you can effectively preserve the integrity of your repaired foundation and minimize the risk of future cracks. Remember, proactive care and attention to your foundation's needs will contribute to a stable and secure home for years to come.
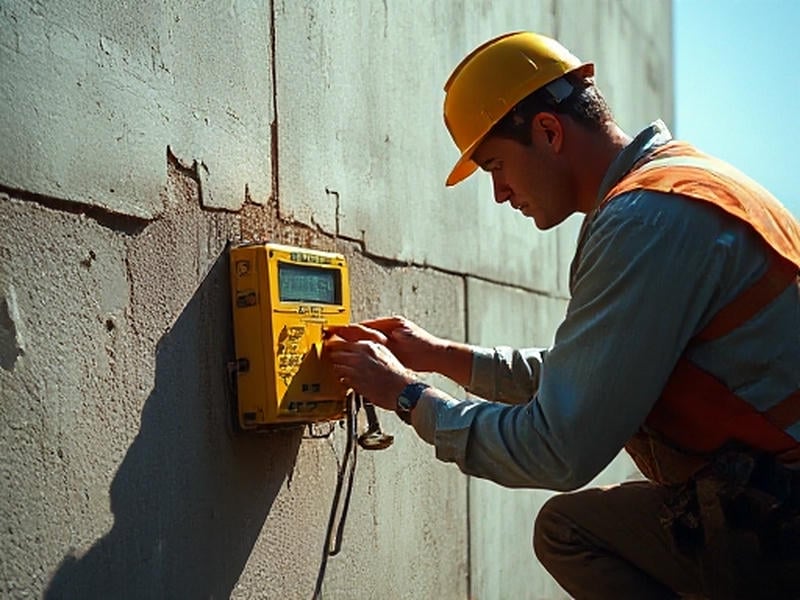